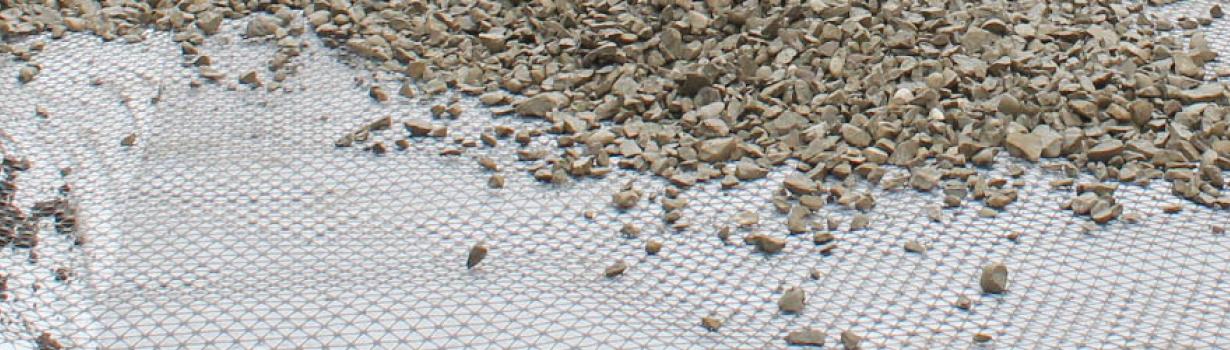
WOBURN TRACKTEX TURNOUT
Rail in NZ runs over a prepared subgrade with adequate subsoil drainage installed parallel to the line, this is then topped with a typical AP100mm broken face hard ballast rock. Sleepers (wooden or concrete) are then placed on top of the ballast with the rail spaced and locked on to the sleepers. When the train passes overhead, the ballast is “pumped” which can cause “mud spots” due to excessive moisture in the subgrade which in turn contaminate the ballast with silts and clays that will work their way to the surface. The consequence of the mud pumping is the loss of rail “line and level” which can lead to reduced speed of the train for safety reasons. This results in expensive return maintenance visits to remedy the issue. Sometimes sand blankets 75mm thick are installed to address this issue, but this is a difficult installation process.
Tracktex™ is a new product in New Zealand and has been used in Australia and the UK to address this issue, and it works very successfully. Turnout areas are the most prone to this issue, due to the frequent crossings by trains and if the area is a clay or silt foundation. One site in Southdown Auckland has already had Tracktex™ installed (700m), this is the next site for KiwiRail to use this product. Geofabrics NZ approached the Wellington office to see if mud spots were an issue, this was one site that was suggested. The installation was done on Boxing Day and the subsequent day, the line was able to be worked on as KiwiRail shut the overhead lines down over this period.
Usually the main construction method is to use a non-woven geotextile with a layer of Tensar TriAx directly on top, which can be followed by another intermediate layer if the subgrade is extremely soft (Tensar TriAx used to prevent differential settlement). Note subsoil drains are still required. Tracktex™ prevents rain water penetrating through to the underlying foundations whilst under load, allowing a controlled upward movement of water through capillary action. It also filters and retains any fine soil particles, in situ, during the process.
The contractor involved is experienced with similar installations under ballast (as above), in this instance the relevant rail sections were first removed by KiwiRail. The contractor then removed the ballast and reshaped the subgrade. Subsoil drains were then cut beside and across (in this instance) the tracks, lined with a non-woven geotextile, and backfilled with P-metal, before wrapping the geotextile over the top.
Tracktex™ (3 rolls of 3m x 25m used on this site) was then installed over the prepared subgrade, any overlaps were a minimum of 1.5m, and Tensar TriAx170 geogrid (2 rolls of 3.8m x 50m used) was then placed directly on top. New ballast was then placed on top of both products and spread by an excavator. The ballast fill level was 340mm, allowing an extra 40mm for settlement. This ballast was placed along with the use of a laser level, with constant readings to ensure the ballast was level and to the height required. New concrete sleeper and rail sections were then placed into the new areas by KiwiRail.
Six staff took approx. 12 hours to remove the ballast, install the drainage and Tracktex™ and Tensar TriAx, place and spread the new ballast.
Two excavators were used (15 tonne and 5 tonne), bearing in mind that they have to operate under the overhead main power lines (turned off at the time of the installation). Two Hydrema dumpers bought in the new ballast as required. A sand layer would take much longer than this, offering the client a significant cost saving.
Tracktex™ is a unique product developed for a specific need to combat water ingress into the railway network, used locally where there is an issue with mud spots, either in turnouts or trouble spots due to the nature of the underlying foundation or drainage issues. The aim is to significantly reduce maintenance visits thus saving the client money and enabling maximum train speed efficiencies.