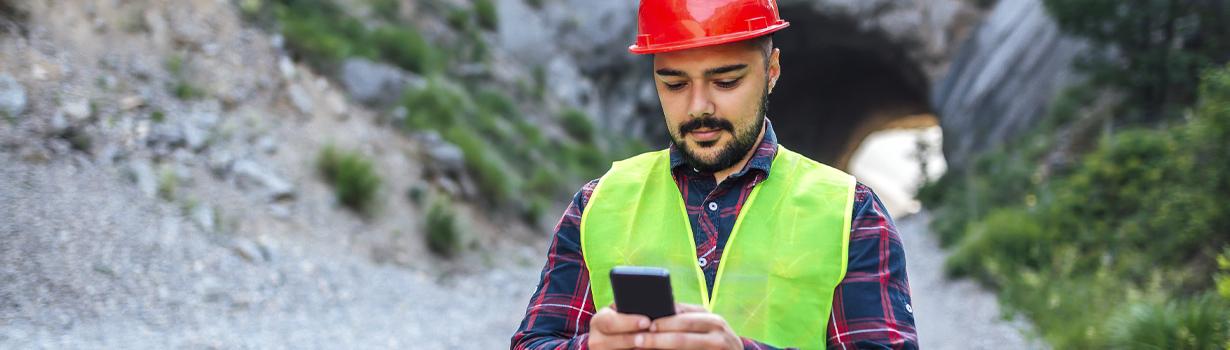
STABILISING A HEAVY-DUTY PAVEMENT WITH MULTIAXIAL GEOGRID
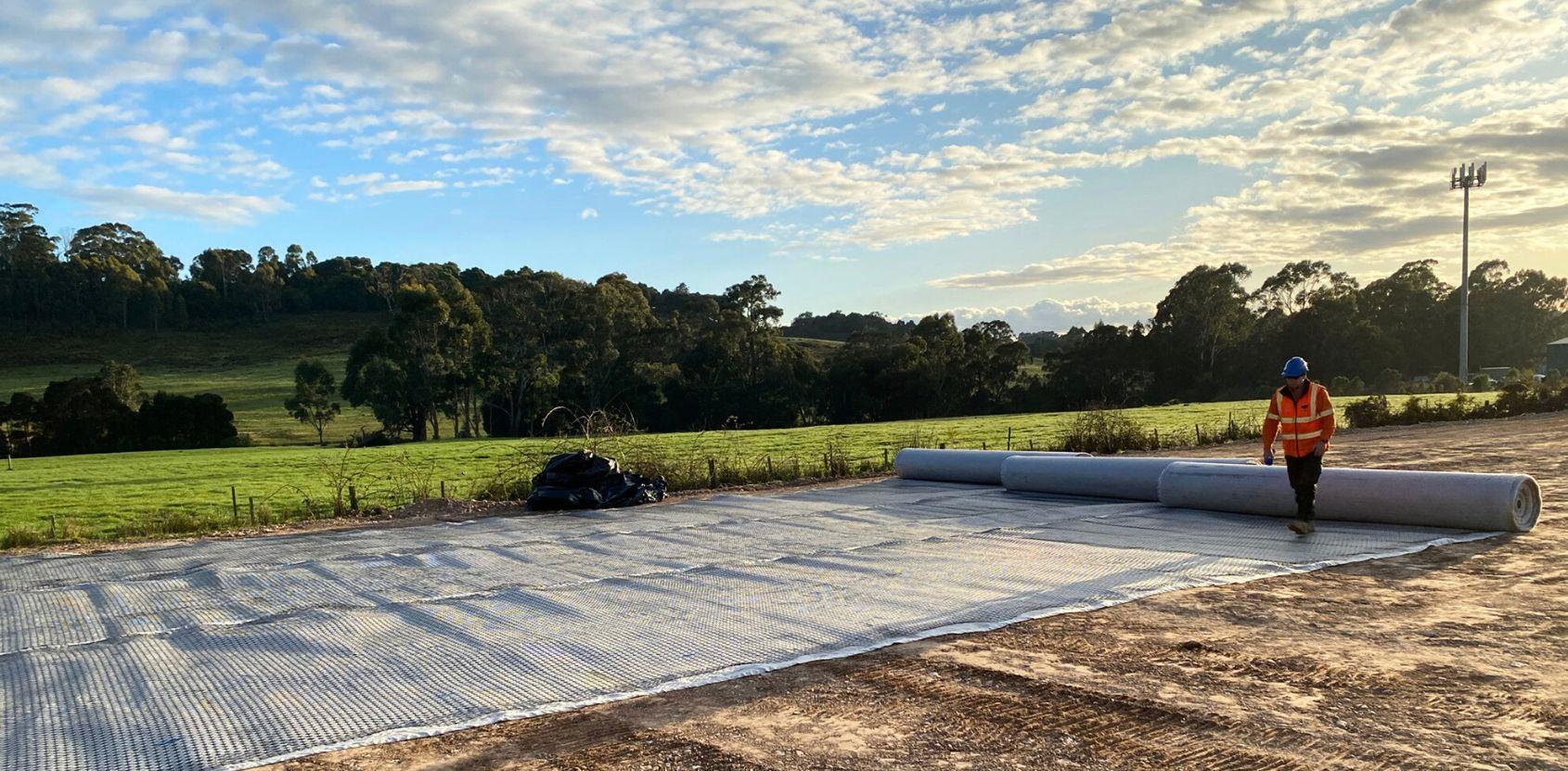
PROJECT DESCRIPTION
The design engineer, Peritas was contacted by Booth Transport to assist with a heavy-duty pavement solution to expand their existing container storage facility in Tasmania. The proposed facility included a new heavy-duty pavement that would be trafficked by container handling forklifts with axle loads of 80t.
OUR SOLUTION
Based on the geotechnical investigation, the initial pavement design was undertaken for CBR = 9%. During construction it was noted that the actual CBR was 7% and some soft spots where CBR = 2.5% were also encountered. To optimise the pavement thickness for the subgrade conditions, a geosynthetic solution was required.
Incorporating Tensar (TX160) multiaxial geogrids into the pavement was proposed as a readily available solution to Booth Transport to minimise downtime on site. Geofabrics and Tensar worked together to propose a solution where pavement thickness did not need to be increased from the original design by using multiaxial geogrid in the pavement. Where soft spots with CBR = 2.5% were encountered, multiaxial geogrids helped to reduce the pavement thickness by approximately 40%, compared to the non-stabilised pavement thickness.
Prior to installation, the existing ground was proof rolled and prepared. Multiaxial geogrid laminated to a non-woven geotextile was installed directly on the subgrade and overlap was provided according to the published installation guidelines. Following this, a 400mm layer of Class 3 subbase was constructed and tested every 200mm. The subsequent layers consisted of multiaxial geogrid and 400mm Class 3 subbase, which was also tested every 200mm with the top layer consisting of 50mm asphalt.
A total of 11,020m² of multiaxial geogrid laminated with non-woven geotextile was used, with an additional 10,545m² of multiaxial geogrid installed. The client was able to avoid construction delays due to weak ground conditions by incorporating multiaxial geogrids into the pavement. For significantly softer areas with CBR = 2.5%, the pavement thickness was reduced by approximately 40%.
PRODUCT USED
Tensar® Multiaxial Geogrid
- Reduces granular layer thickness and CO₂ emissions in construction by up to 50%
- Cost savings in foundation material required to build working platforms by up to 50%
- Durable structure that provides greater stability and stiffness in challenging weather and environmental conditions
- Multiple layers form a stiff beam that spreads heavy loads over a larger area, reducing differential settlement
- Can be installed quickly, reducing construction costs when building all pavement types over soft ground for standard and heavy vehicle loads

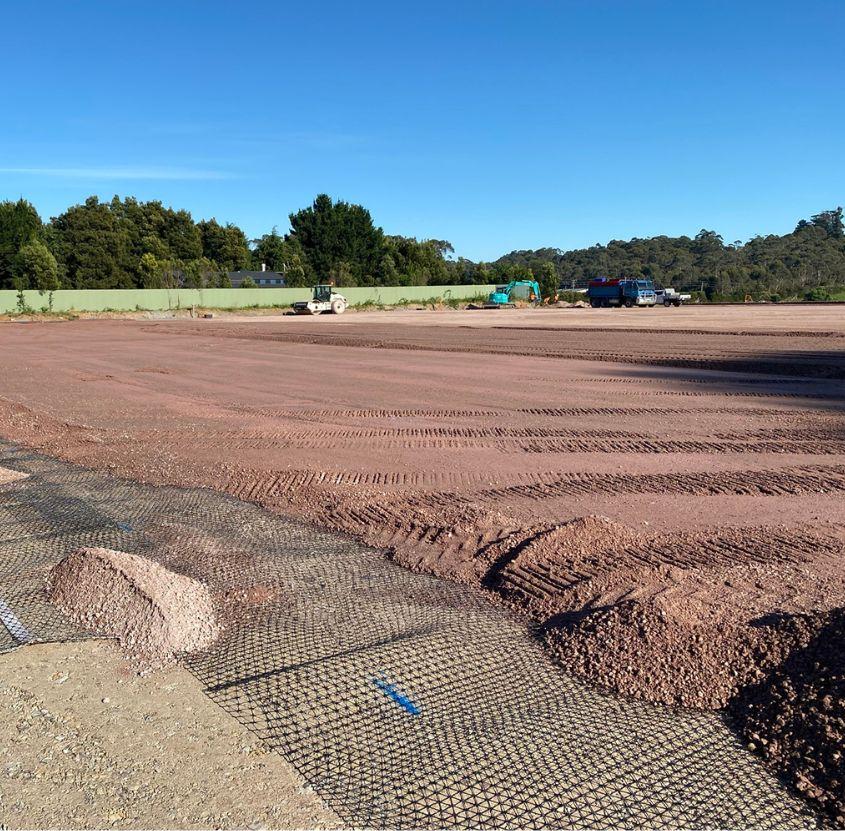