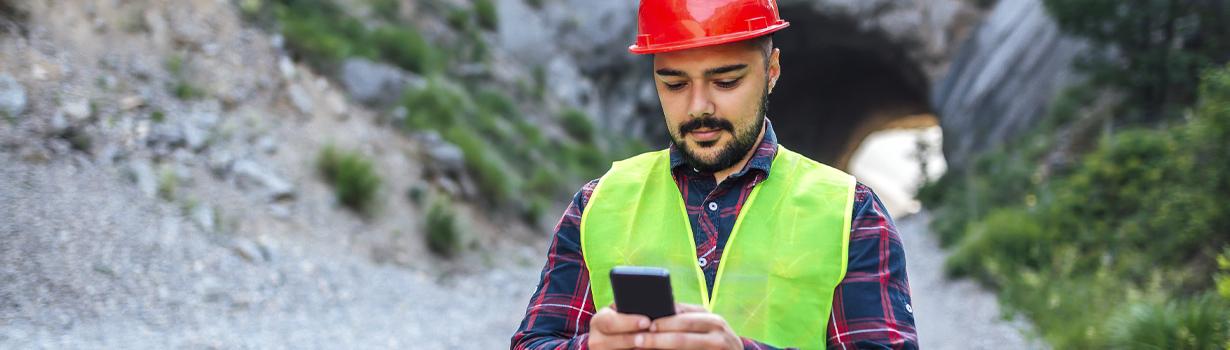
REDUCING THE THICKNESS OF A WORKING PLATFORM WITH TENSAR INTERAX
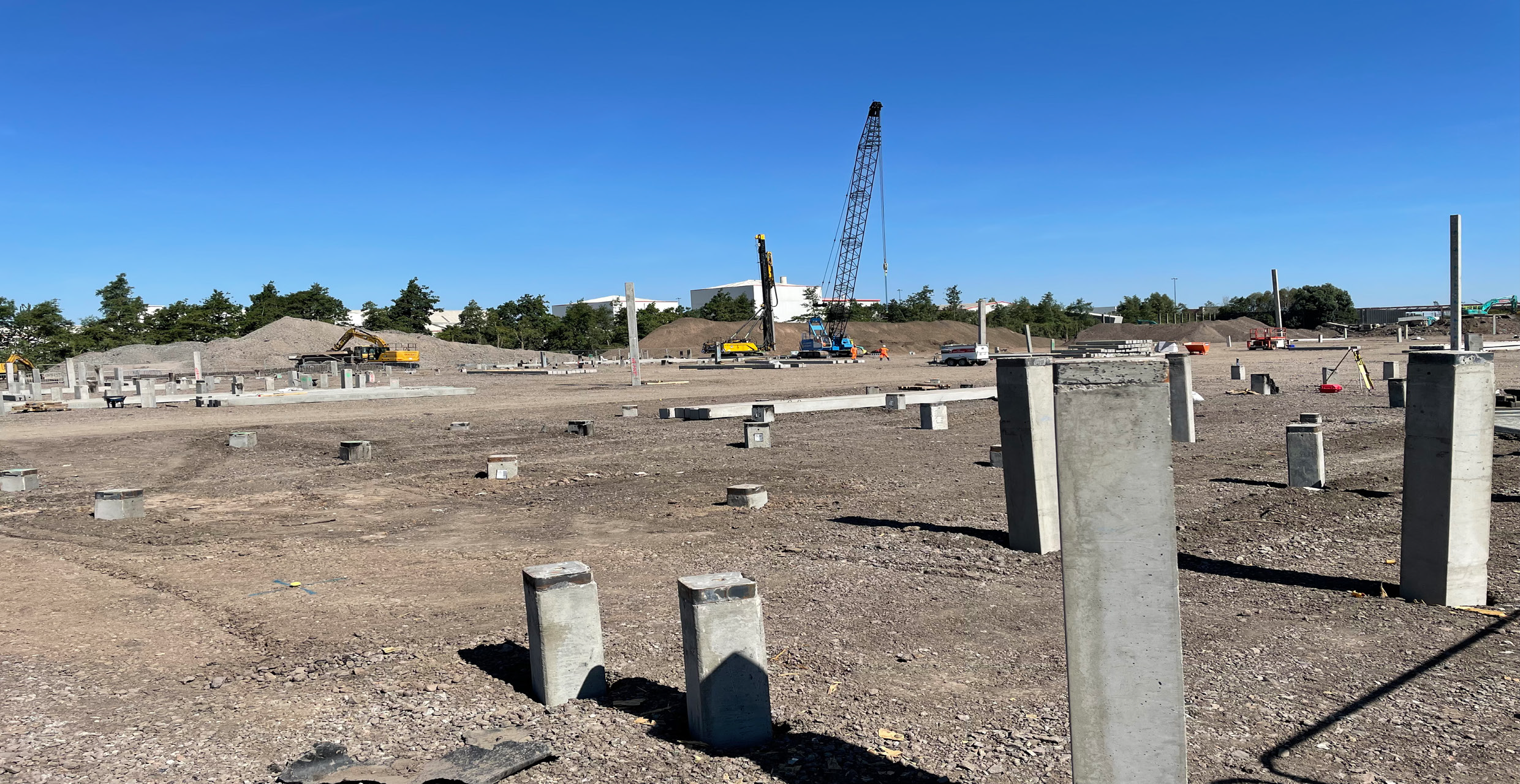
PROJECT DESCRIPTION
A working platform was required to address the poor ground conditions for the extension to the ETEX factory in Bristol. A Tensar mechanically stabilised platform was adopted to provide a cost effective and technically suitable solution for the client.
The site comprised of poor ground overlying tidal flat deposits and a high water table was also present. Despite this, the platform thickness had to be reduced from initial designs and be fully constructed from recycled material reclaimed from within the site.
OUR SOLUTION
The Tensar proposal achieved a 60% reduction in platform thickness when compared to the proposals available using the illustrative calculation method described in BR470.
The Tensar mechanically stabilised platform, incorporating a Tensar stabilisation geogrid was designed using the Tensar “T-Value” approach which applies Tensar’s extensive, credible and representative research into how geogrid acts within the platform material.
To avoid the need to import granular material, recycled material was recovered from the site and used to form the mechanically stabilised platform. The piling operations were subsequently successfully completed.
PRODUCT USED
Tensar® InterAx® Geogrid
- Speeds up construction, saving up to 70% in aggregate section reduction
- Optimised geometry design for maximum confinement and compaction of granular fill, creating the most efficient mechanically stabilised layer (MSL)
- Improves compaction and restrict the movement of the particles over time, retaining the stiffness long term and further enhancing performance of the MSL
- Results in a more resilient solution that will withstand severe weather events, the increasing impact of climate change, and other challenging environmental conditions
- Improves interaction between the geogrid and aggregate for better performance
- Less aggregate is required to meet project requirements, which leads to savings on cost, time and carbon emissions
- Ideal for subgrade stabilisation, roads, heavy-duty pavements, and working platforms