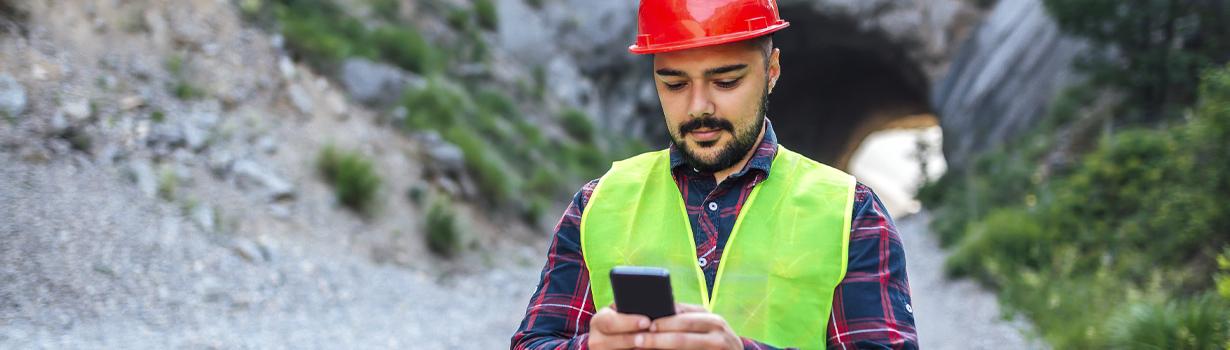
FEA AND THE LI-SELIG METHOD IN RAIL DESIGN
New design methods to incorporate stabilisation geogrids into railway trackbeds could save time and costs over the lifecycle of the asset.
Around the World passenger rail numbers have been growing consistently and rail authorities are forecasting passenger rail demand to continue increasing. This, combined with continued reliance on rail networks for freight capacity, will increase pressure on railway infrastructure in the coming years, especially in terms of track reliability.
Rectifying poor track geometry caused by subgrade and ballast deformation often results in speed restrictions being imposed and unplanned maintenance work. Use of geogrids for trackbed stabilisation to minimise rail alignment issues is a proven approach but a new design method by Tensar could enhance capabilities further.
While geogrids have been used for decades in rail track construction, current performance-based design methods do not accurately predict long term behaviour.
“The need for trackbed maintenance work and line speed restrictions are expensive and disruptive to the public, industry, train operators and asset owners,” says Tensar senior application technology manager, Andrew Lees.
“Mechanical stabilisation of sub-ballast layers using geogrids is a tried and tested approach that can reduce maintenance, by reducing traffic-induced degradation, slowing the rate of track settlement, maintaining track geometry for longer and extending ballast life 10-fold.”
According to Lees, maintenance intervals can be up to three times longer. “Reducing whole-life costs, in terms of both cash and carbon,” he says.
However, while geogrids have been used for decades in rail track construction, current performance-based design methods do not accurately predict long term behaviour of ballast, sub-ballast and the subgrade, which means their benefits cannot be truly modelled during design.
“We set out to resolve the design-related issues, with the aim of developing a new design method that not only predicted track foundation performance more accurately but that would also allow the benefits of installing stabilising geogrids to be determined reliably,” explains Lees.
“The Li-Selig method is the common approach used in performance-based track design. This is used to predict permanent subgrade deformation, based on empirical relationships and analysis models developed in the 1970s.”
Tensar’s initial investigations used finite element analysis (FEA) with elasto-plastic constitutive models, instead of the linear elastic models of the older analysis methods. This work highlighted some of the drawbacks of using this approach.
In particular, the team found that, compared with other input parameters, permanent deformations were not particularly sensitive to the stiffness of subgrade and ballast layers – which are key input parameters to the elastic layer analysis used in the Li-Selig method.
“It was found that predictions were highly sensitive to the depth of the subgrade layer and the properties of the underlying soil layer, making an appropriate selection of the subgrade depth in the Li-Selig method almost impossible,” says Lees. “As a result, the approach was rarely found to deliver an accurate prediction of trackbed behaviour.”
Lees says that Tensar’s approach uses advanced, but readily-available, hardening plasticity models to predict permanent subgrade deformations under train wheel loading.
“These outputs are multiplied up by the more reliable element of the Li-Selig method that depends only on the subgrade soil type to obtain a prediction of the accumulation of subgrade deformation under successive train loading,” he says.
“The method also includes a simple mobilised bearing capacity calculation for optioneering, rather than having to carry out a full 3D FEA, which can be time-consuming and expensive, if used on every design option.”
Relationships have been derived between mobilised bearing capacity and permanent subgrade deformation that can also be multiplied up to obtain approximate predictions under successive train loading.
“Once the preferred option has been chosen, a full FEA model can be run,” adds Lees.
Tensar’s new approach was calibrated with its Triax geogrid, using laboratory testing carried out at the Czech Technical University, with 500,000 load cycles on rails and sleepers supported by stabilised and non-stabilised sub-ballast over a clay subgrade.
Data gathered by Tensar and its research partners during full-scale field trials of geogrid placed in sub-ballast on live freight and passenger lines in Slovakia, the US and South Africa was used to back-analys, and confirm modelling predictions.
Lower quality materials, such as fouled ballast, stabilised with Triax were also tested and it was found that their stabilised mechanical properties exceeded those of non-stabilised, higher quality materials.
“This could have a major positive impact on costs and sustainability, as it enables re-use of fouled ballast materials as sub-ballast, in both new track construction and rehabilitation,” explains Lees.
“With an ever-increasing burden being placed on rail infrastructure, there is clearly a need to deliver safe permanent way efficiently, with designs that offer value for money – in terms of both construction and whole life costs – and that have minimal environmental impact. This essentially boils down to mitigating risk – a large proportion of which lies in the ground. Of course, it is incredibly difficult to predict every possible situation arising during construction and operation but more accurate modelling, which enables track engineers to design to actual ground conditions, can deliver more appropriate solutions, mitigate risks and ultimately add more value.”
According to Lees, this new design approach enables designers to more accurately predict long term subgrade deformation and to model the benefits of incorporating stabilising geogrids into sub-ballast. “This should save time and money during construction and over the operational lifetime of a railway, through longer maintenance intervals,” he concludes.
BALLAST BENEFITS
When granular fill material, such as ballast or sub-ballast, is compacted over a geogrid, it partially penetrates and projects through the geogrid’s apertures to create a strong and positive interlock. This interlock enables the geogrid to confine and restrain the granular material from lateral spread, which helps maintain horizontal and vertical rail alignment.
Laboratory and field testing has shown that sub-ballast layers stabilised by geogrid are better able to distribute imposed traffic loads, by increasing the area of influence on the subgrade, so bearing pressures are lower.
By providing a stiffer foundation to the track, settlement has been reduced by almost 40%, for the same amount of rail traffic, compared with non-stabilised sub-ballast layers. These layers can also be up to two-thirds thinner, while maintaining bearing capacity, reducing excavation and replacement of weak subgrades, cutting construction time and costs.
Track profiles can also be smoothed at interfaces between structures, for example where embankments meet concrete trackbeds beneath overbridges and in tunnels, by reducing the effects of differential settlement.
This article was originally published on the Ground Engineering website on the 17th of October 2018. You can view the original article here.