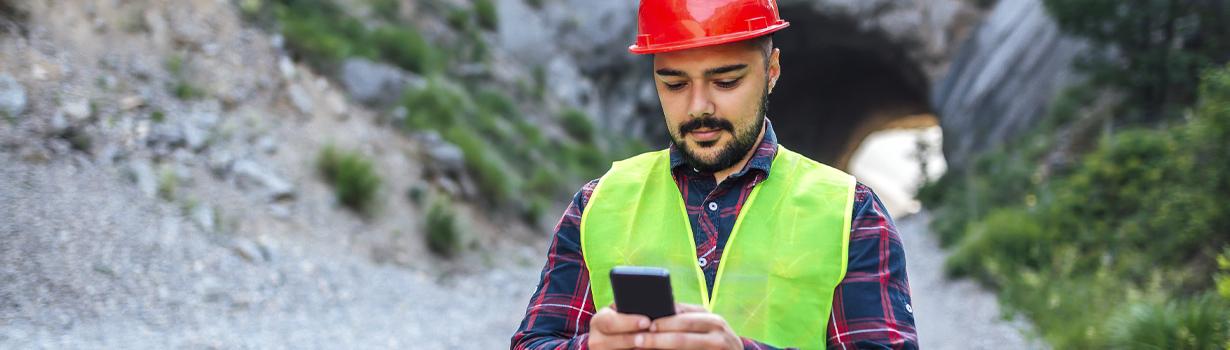
CONTROLLING SPILLING SEDIMENT AND TAILINGS INTO THE ENVIRONMENT
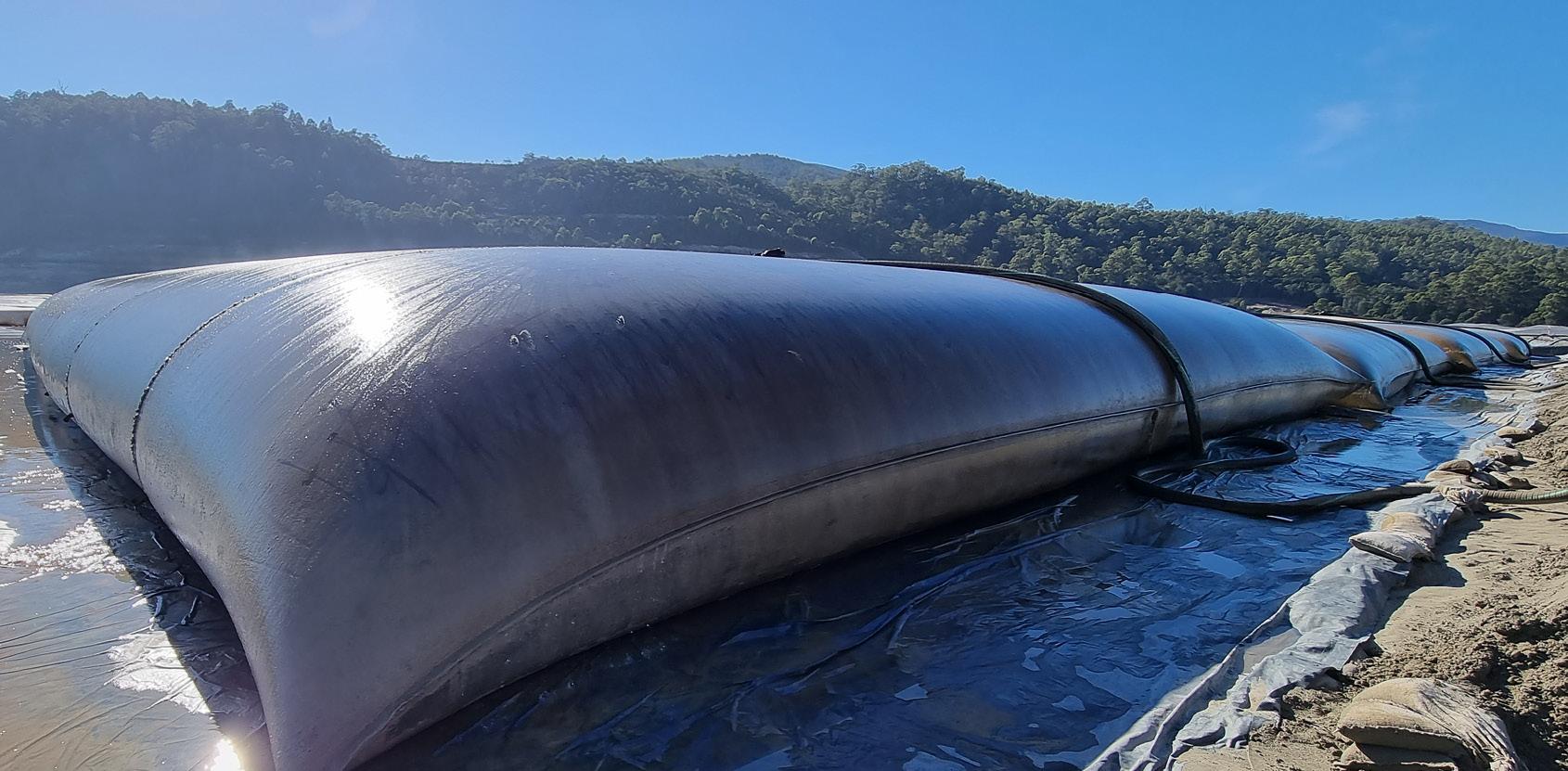
PROJECT DESCRIPTION
The MMG Mine in Rosebery is located approximately 300 kilometres north-west of Hobart, Tasmania. The mine has been operating for nearly 80 years, with operations commencing in 1936.
The mine was nearing capacity of the Bobadil Tailings Storage Facility (TSF), and an embankment raise was required in order to increase the dam’s capacity and allow for continued processing and expansion of the facility. The project took place from August 2020 until early 2021.
A turbid wastewater with roughly 0.5% solids content was still being discharged into the 1,000m x 650m TSF, and was starting to block the overflow channel which was also close to its limit.
To prevent the channel blocking, a system was required to collect the sediment prior to it reaching the overflow channel. Any blockages would risk overtopping the TSF in an uncontrolled manner, spilling sediment and tailings into the polishing ponds and eventually the environment.
OUR SOLUTION
To resolve the challenges on site, the TenCate Geotube Dewatering Container was seen as the ideal solution. It was scalable, had a relatively low upfront capital cost and could produce clean filtrate water when combined with a suitable flocculant and polymer dosing rig. Due to their international experience with similar applications, Geofabrics and TenCate were engaged by Armstrong Resource Management, the dredging contractor, for technical support.
In order to properly assess the viability of this concept, Geofabrics tested a sample of the wastewater from site using their in-house Geosynthetics, Research, Innovation & Development (GRID) lab on the Gold Coast. This testing service was offered to illustrate the performance of the sludge type with various flocculants and the Geotube geotextile. The testing gave the customer confidence that the sludge would dewater well in the bags, as well as retain and capture the solids producing an acceptably clean filtrate.
Following testing, the Geofabrics team in conjunction with TenCate carried out a site-specific proposal that considered wastewater material properties, flow rates and helped predict final dewatered volumes. In addition, Geofabrics were able to produce a conceptual layout for the Geotube units over the tailings dam.
The MMG Mine project was a unique case due to the location in the middle of dense forestland providing limited space for the laydown area normally critical for Geotube applications. Due to the nature of the site the only option was to lay the bags over the tailings surface of varying strength and not on level ground. Geotube units typically must be laid on level ground to prevent risk of rolling. The risk was considered minimal and fill heights were managed and monitored to suit the varying ground conditions. It was understood that there were very few options that would allow processing to continue and wastewater to flow into the TSF.
This innovative solution was easily scalable and cost effective. Trials onsite for desludging the adjacent polishing pond also reinforced the Geotube concept.
Technical support from Geofabrics and TenCate on Geotube dewatering projects is a unique source of information for both stakeholders and installers/dredging operators. Add to that the international experience across various large mining operations, there is significant value in getting Geofabrics’ involved in dewatering concepts only.
PRODUCT USED
TenCate Geotube® Dewatering Container Geotextile
- Also known as geobags, are used for sludge dewatering projects of all sizes
- No belts, gears, or complicated mechanics, it is available in many sizes, depending on volume and space requirements
- Can be mounted in mobile roll-off containers that can be transported around your property
- One of the most versatile dewatering technologies available
- GT500-366-306-B2P08 units were used, which are manufactured from GT500 woven monofilament and fibrillated geotextile, suited for dewatering that does not compromise pore size when under tension
- Made using polypropylene yarn which is inert to most water chemistries
- Can store up to 1,000m3 of material, being 30.6m long by 18.3m wide when laid flat
- Circumference of the bags are 36.6m, with each unit containing 2x200mm PVC flange filling ports
- Have a high seam strength to allow for high pump heights, which in turn creates larger volumes per sqm of footprint and induces a higher factor of safety during pumping to meet site specific requirements
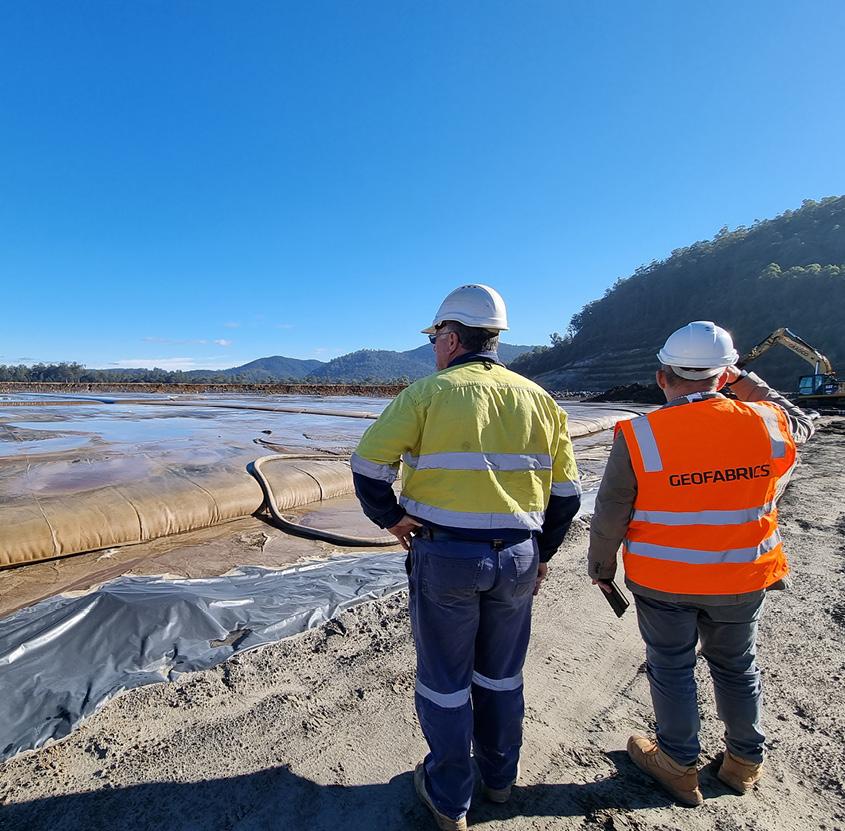
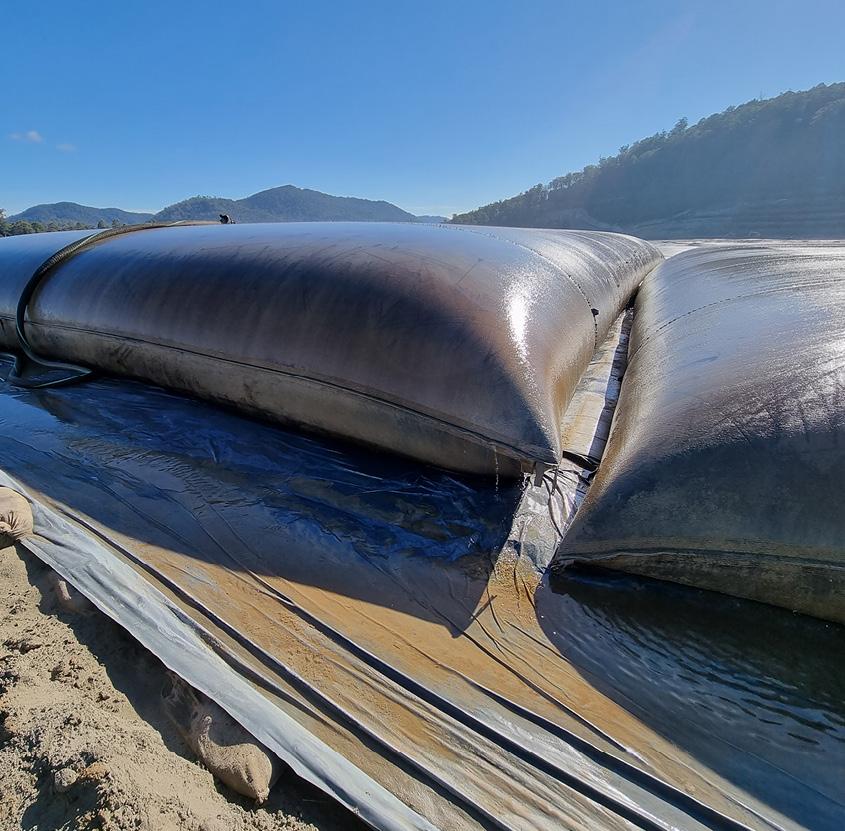