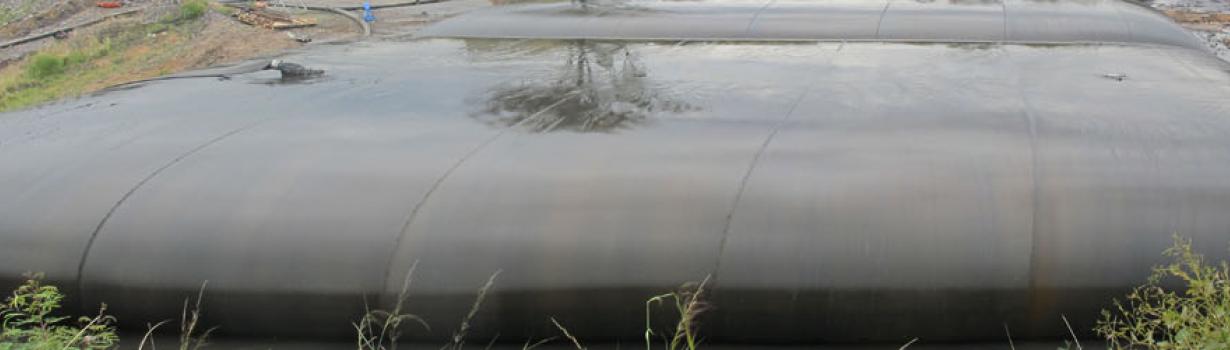
Coal Fines Sludge Dewatering
The Yancoal Australia Hunter Valley Operations (HVO) is a multi-pit open-cut mine producing more than 13 million tonnes of thermal coal and semi-soft coking coal using dragline truck and shovel methodology. The raw coal that is mined is called the run-of-mine (ROM) coal is delivered to the Coal Handling and Preparation Plant (CHPP).
Typically 17-20% of the ROM coal delivered to the CHPP is considered waste. This facility washes the coal of soil and rock, crushes it into graded sized coal, stockpiles and prepares it for transport to market. The more of this waste material that can be removed from coal, the lower its total ash content, the greater its market value and the lower its transportation costs.
After being washed and prepared for sale, the coal is loaded onto trains for transportation 90 km to the Port Waratah Coal Terminal in Newcastle where it is shipped to international customers.
The waste slurry from the CHPP, is directed into settling ponds or tailings dams, however in order to reduce waste, many mines recover the coal fines for further processing. The slurry can either be processed in a series of centrifuges and cyclones to remove water and separate the coal fractions however this is an expensive mechanical process. An alternative is to use dewatering technology using Geotube dewatering containers and Yancoal Australia decided this was the best option for the HVO north pit at Ravensworth.
The settling pond was approaching a level that meant it could no longer accept further solids without the risk of overflowing. Consequently, Dredging Systems Pty Ltd was engaged to remove the sludge so that the coal fines could be recovered. A small dredge was used with a rotating cutting head on the inlet pipe. This enables the sludge to slurry in the base of the pond and enables the collection of solids to be accelerated.
The sludge was then pumped into eight Geotube dewatering containers supplied by Geofabrics Australasia. These tubes, contained in a large bunded area adjacent to the settling pond, had a circumference of 36.6 m and were 30.6 m in length with capacity to retain a dry volume of approximately 1,000 m3 of dry cake.
Each tube was connected via a pipe manifold system so that as one Geotube reached its maximum fill height, the valves could re-direct the pumped slurry into the next tube. As each Geotube cycled through pumping and dewatering sequences, the containers progressively retained the coal fines up until each tube could no longer accept further solids without extending beyond their maximum fill height. Effluent water from the tubes was returned to the settling pond via channels inside the bund wall surrounding the Geotube containers.
Each Geotube container was supplied with two filling ports. These ports could either be a fabric port or one with a PVC Geoport reinforcing collar. In this instance, due to the size of the containers, PVC ports were supplied. Lay-flat hoses were used to connect into these ports to maximise flexibility of the hoses as the Geotube is pumped into and the Geotube inflates without putting strain onto the filling port.
Often, polymers are added into the manifold pipework which enables very fine colloidal fractions to form a floc and promotes rapid separation of water from solids to accelerate the dewatering process. In the case of the HVO pond, the addition of polymer was not required and the process progressed at a satisfactory rate. After three months, the retained solid material within the Geotube containers had sufficiently dewatered allowing the Geotube to be split open and the ‘cake’ easily removed using a loader and sent for processing and on-sold.